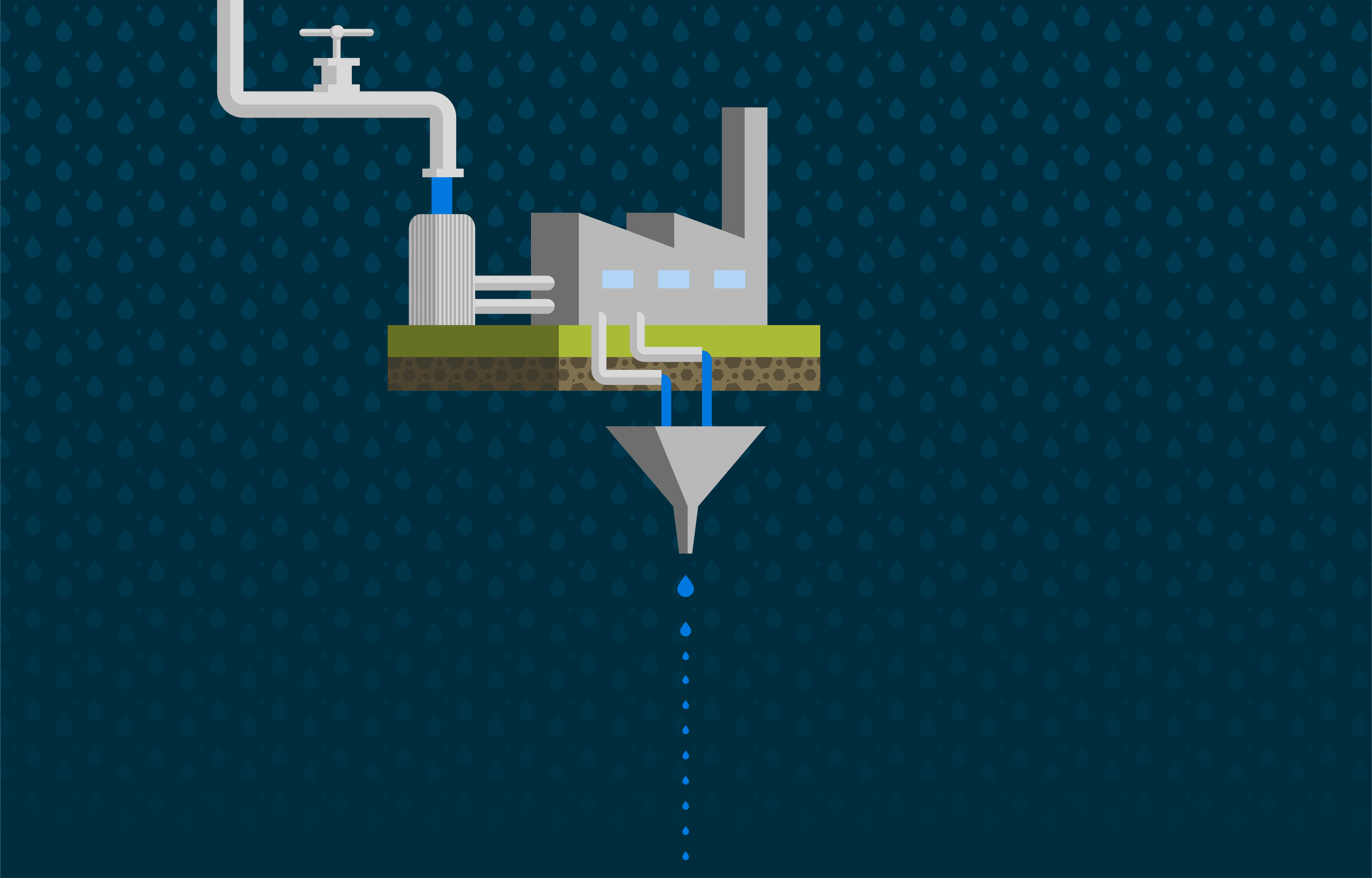
Podcast: ReUse - Use the wastewater
Many manufacturing companies use water in their processes. A lot of water. In this podcast from 2024, the Danish Technological Institute and Viegand Maagøe look at solutions to recover and reuse process and wastewater from large Danish manufacturing companies.
About the ReUse project
ReUse is a project from MUDP – the Danish Environmental Protection Agency’s pool for environmental technology development and demonstration projects.
The ReUse project is central to finding solutions to recover and reuse process and wastewater from large Danish manufacturing companies.
ReUse uses a completely new mapping method and innovative technologies to demonstrate how wastewater does not have to go to waste, but can constitute a valuable resource in Danish manufacturing companies. In the podcast we follow the project from start to finish.
Section 1 - The keyword is upstream
In this episode, we talk to Christian Fischer from the Danish Technological Institute, Fridolin Holm from Viegand Maagøe and Nanna Rørbech from the Danish Environmental Protection Agency about why the ReUse project is a beacon in the field, and what the project is actually about.
Episode 2 - Brothers Hartmann: The water can no longer be reused
We visited the egg tray manufacturer, Brdr. Hartmann, in Tønder, to talk to them about their participation in the ReUse project. A participation that is not going quite as expected...
Section 3 - CP Kelco: 1.5 million liters of water for recycling
In this episode, we visited the pectin factory CP Kelco in Lille Skensved to find out how much recycling potential ReUse has helped to realize in their water-intensive production. Hint: It's not that small. The savings potential is large, and the project is even only at demonstration level.
Episode 4 - Nopa Nordic: Fulfilling great potential
We are visiting Nopa Nordic in Hobro, which does everything within cleaning production. In their production there is great potential to reduce product waste, save water, and send cleaner wastewater away from the factory. It has been especially eye-opening for Nopa to map their production to find out where it could be optimized.